In the rapidly expanding world of electric vehicles (EVs), Cox Automotive’s innovative ‘Flying Doctor Program’ has emerged as a pioneering force in ensuring safety, sustainability, and expertise. The flying doctors zip across the United States, able to be on location in as little as 24 hours to address emergency battery-related incidents in automotive dealerships and on the road. Their focus includes rapid and expert interventions, safe handling, recycling of damaged battery materials, and proactive risk reduction in potential hazard scenarios.
As part of the growing portfolio of services offered by Cox Automotive, the Flying Doctors are contracted to service OEMs, dealerships, and major clients, adding another dimension of care and support in the evolving EV landscape.
“Evolution in the EV sector demands both innovation and precaution. With the Flying Doctor EV Program, we're addressing today's challenges and paving a safer, sustainable path for tomorrow. It's our commitment to ensuring that as EV technology accelerates, so does our dedication to safety, sustainability, and service excellence.” — Lea Malloy, AVP of EV Battery, Cox Automotive
A Drive into the Origins
The idea behind the program stemmed from a simple yet powerful vision from Cox Automotive – assisting and resolving challenges for business partners and colleagues. Brandon Carter, an engineering manager and key program member with nearly a decade of experience in the EV sector, expressed how early exposure to various roles, from fabrication to customer relationships, crafted their reputation as problem solvers. The very essence of this initiative revolves around providing solutions. It’s worth noting that this innovative program was a response to customer requests based on Cox Automotive’s experience in the EV remanufacturing market.
"We envisioned a program rooted in a simple idea: wanting to assist and create resolutions for not just our business partners but our colleagues too." — Brandon Carter, Engineering Manager, Cox Automotive
A Sustainable White-Glove Service with Rapid Response
Providing a white-glove experience, the program dispatches experts to service damaged EV batteries across the United States. Currently, they are actively under contract for one OEM, and with their outreach extending to over 20+ dealers, they expect more OEMs to come on board in 2024.
After receiving the client’s call and arriving on the scene, the doctors address the initial emergency and ensure the entire battery structure is safely discharged, meticulously broken down, and packaged. Every component is then transported back to facilities where it’s recycled, ensuring minimal waste and a nod to sustainability. “We ensure nothing is lost. From metals like aluminum, copper, and steel to lithium, every usable component is reincorporated,” said Carter.
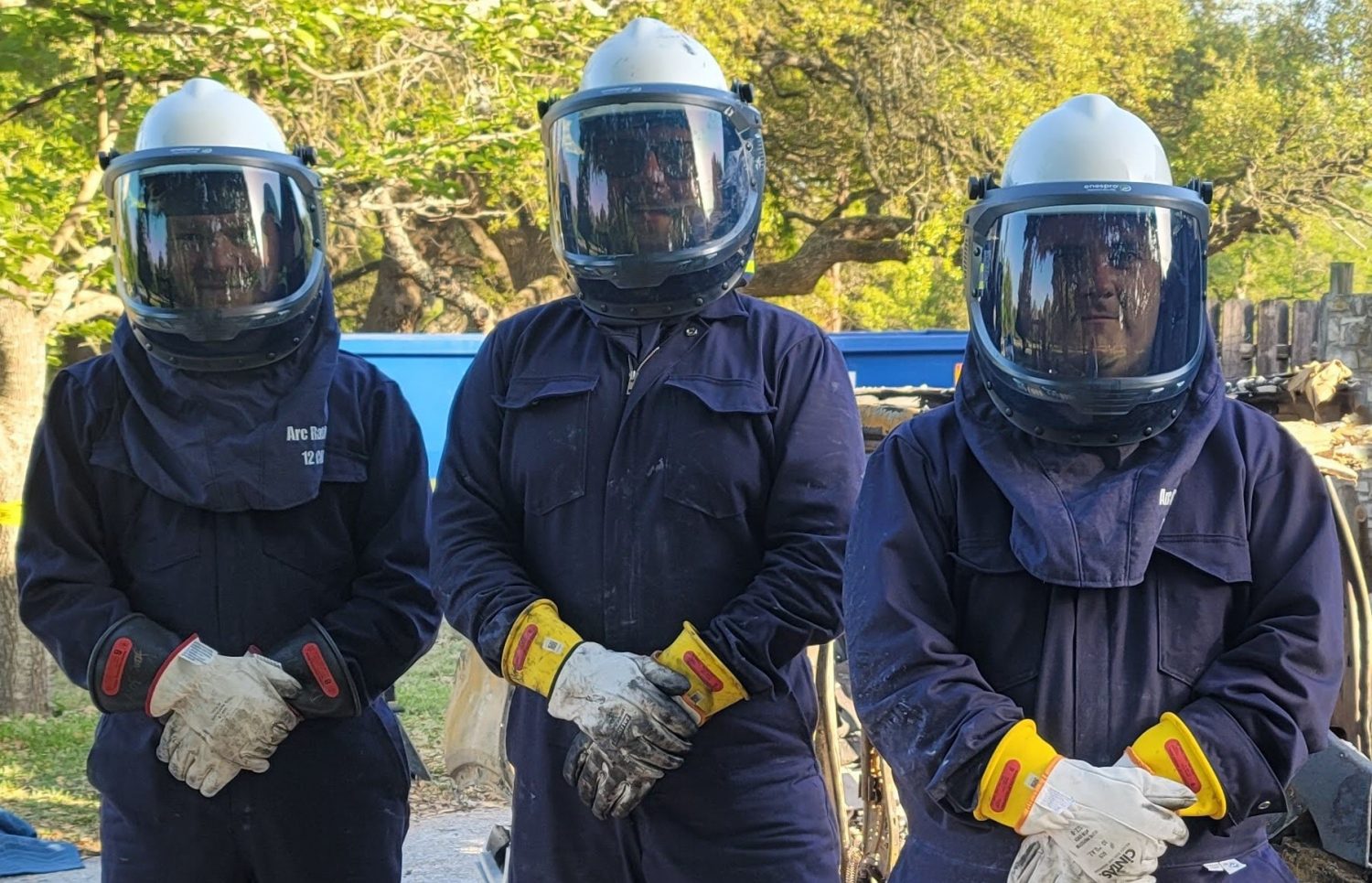
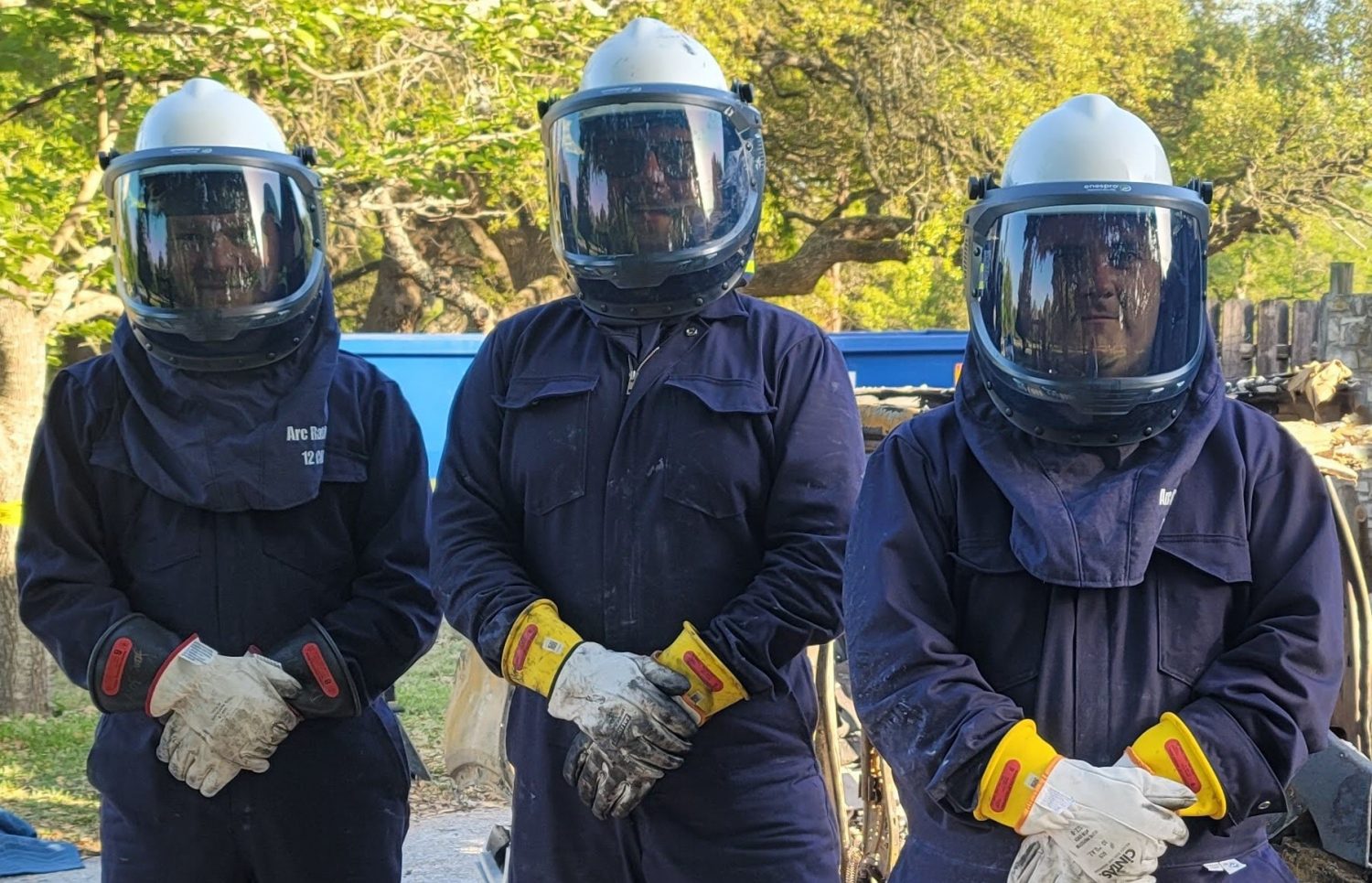
From left to right: Kevin Wilds, Brandon Carter, and Matthew Davis travel across the United States to safely manage any EV battery mishaps.
"Ensuring the safety and sustainability of the EV landscape is not just our mission; it's our passion. As the electric vehicle sector grows, so will our commitment to offering rapid, expert intervention and championing a future where every battery finds a second life in recycling.” — Lea Malloy, AVP of EV Battery, Cox Automotive
From Broad Range to Precision
Despite the array of battery types and sizes – from off-road vehicles to high-end sports cars – the team’s approach starts with consistent foundational steps. This involves thermal camera activation to detect battery hotspots and closely monitoring these for potential risks, such as hazardous runaway thermal events.
In such an event, the procedure is to alert first responders and quarantine the area. The doctors’ primary response isn’t firefighting but risk reduction after an event. Suppose a thermal runaway event is not detected. In that case, the team disassembles batteries on-site, ensuring they are safely discharged, becoming inert, and subsequently returned for recycling.
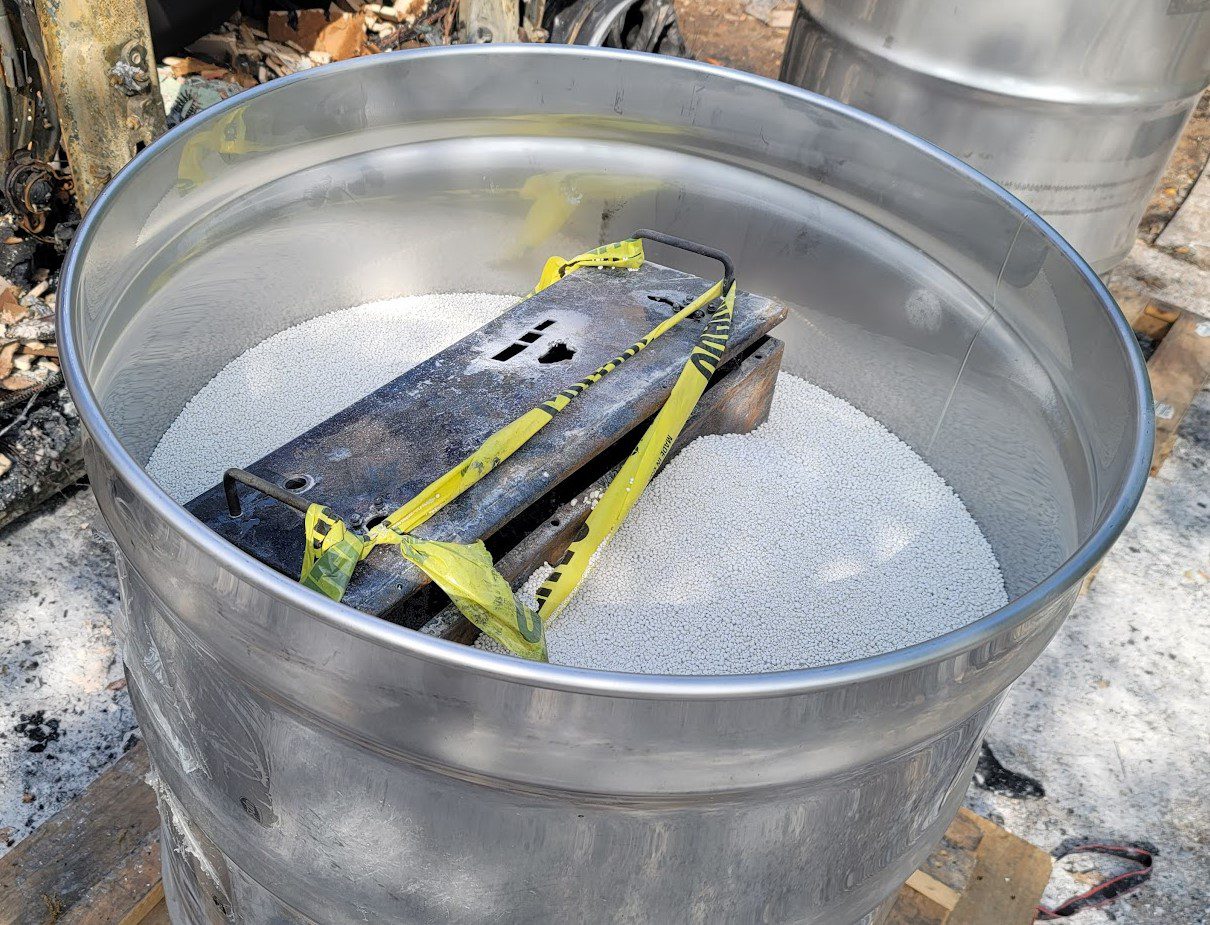
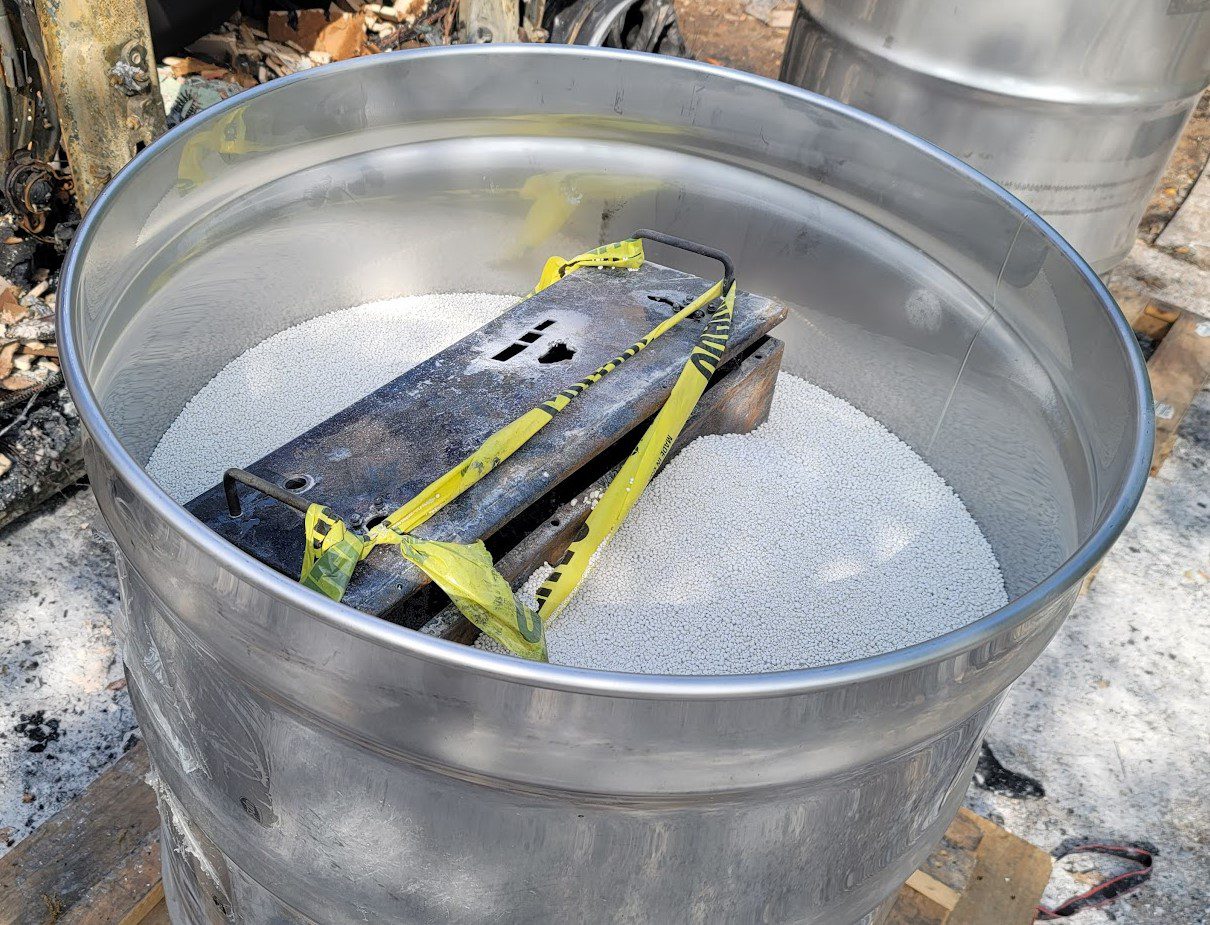
In this energy storage system, featuring a stainless steel drum filled with pyro bubbles that the doctors bring on site, any heat or fire risk can be effectively neutralized. The insulating layer ensures the exterior remains cool even if the interior is hot.
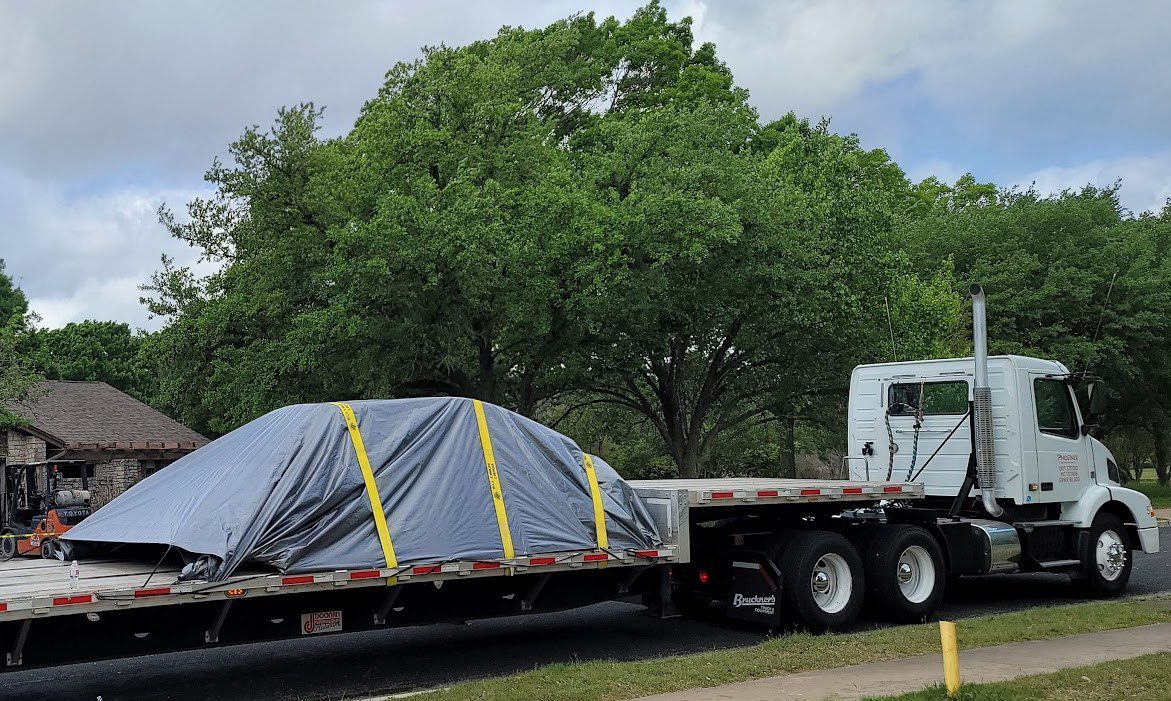
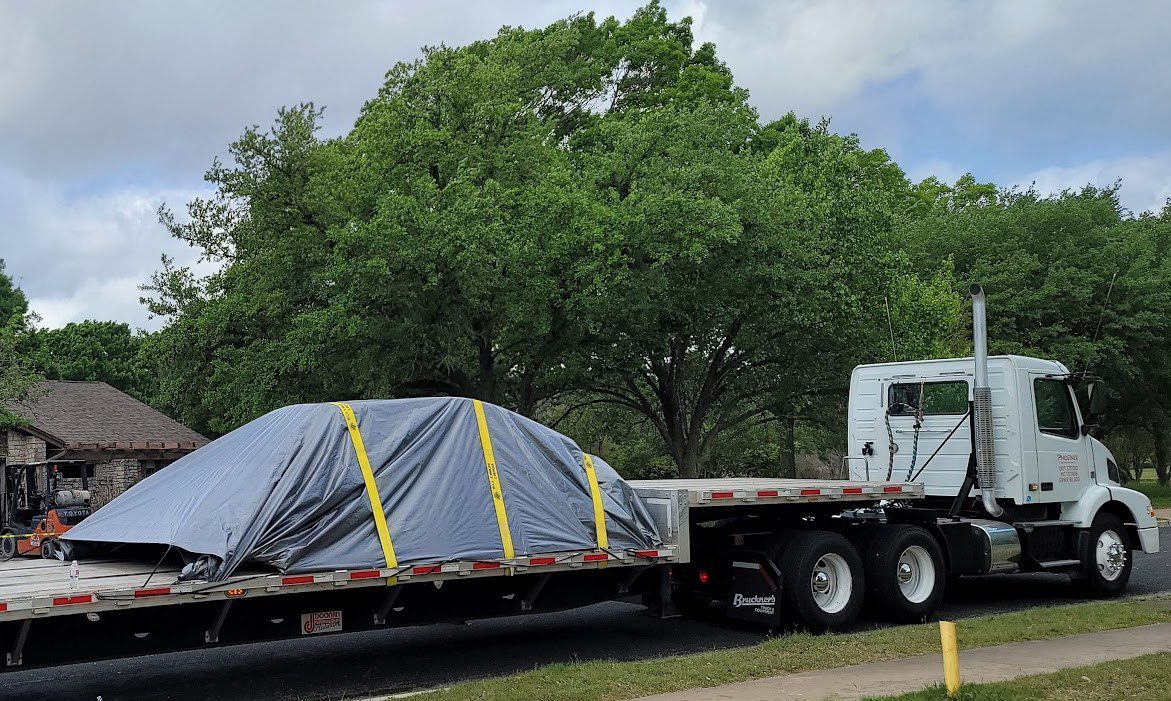
This image shows a vehicle prepped for transport after the Flying Doctors conducted a research study in collaboration with the NFPA in Austin, TX. The vehicle was intentionally placed inside a house with a garage set to ignite as part of the experiment. Their task was to extract the lithium, remove the battery from the car, and transport both separately. The car was also later recycled.
Emergency Protocols in Action
The program’s emergency response times are truly commendable. Contracted work typically receives a notice of three to five days. However, the response can be whittled down to just 24 hours in dire situations. Potential emergency scenarios like battery short circuits during production or road incidents require a rapid response time.
Training and Expansion: The Path Forward
Currently, the core team comprises three dedicated members, led by Carter. All members undergo rigorous training, emphasizing real-life battery dangers.
“We primarily seek individuals from the automotive technician industry, those adept with electrical components. This role requires a blend of exceptional technical know-how with engineering acumen. Many automotive technicians, though hesitant about the EV realm, already possess the requisite skills.” — Brandon Carter, Engineering Manager, Cox Automotive
While formal training methods are beneficial, the program leans heavily towards on-the-job training, underscoring real-life dangers and battery considerations. New entrants shadow experienced members until they attain proficiency.
Track Record
Having conducted operations for over two years, the Flying Doctors made approximately 30 runs since the program’s inception in 2021. The more formalized contract work began at the start of 2023.
Leading the Charge: Safeguarding the EV Battery Frontier
Though most of their work predominantly occurs at dealerships, the team’s dedication transcends boundaries. Their operations underscore the significance of safety, training, and sustainable practices. This initiative is a testament to Cox Automotive’s broader effort to expand its EV battery services, solidifying its goal of becoming the world’s largest automotive services provider. In an age dominated by electric propulsion, the Flying Doctor Program stands tall, not just attending to emergencies but also championing sustainable advancements in the EV landscape. As a testament to Cox Automotive’s unwavering commitment, this initiative ensures the well-being of EV users, technicians, and our environment alike.